Pillow Manufacturing SaaS solution to fully manage all your manufacturing needs
Details
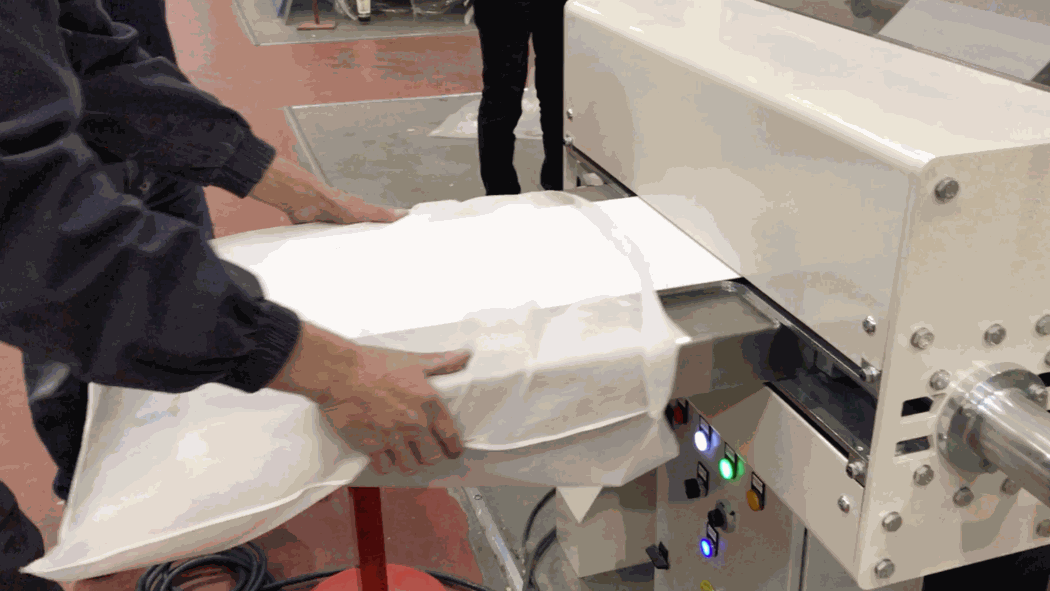
An ERP system tailored for pillow manufacturing streamlines operations improves efficiency, and enhances profitability. It integrates various business functions into a centralized platform for managing:
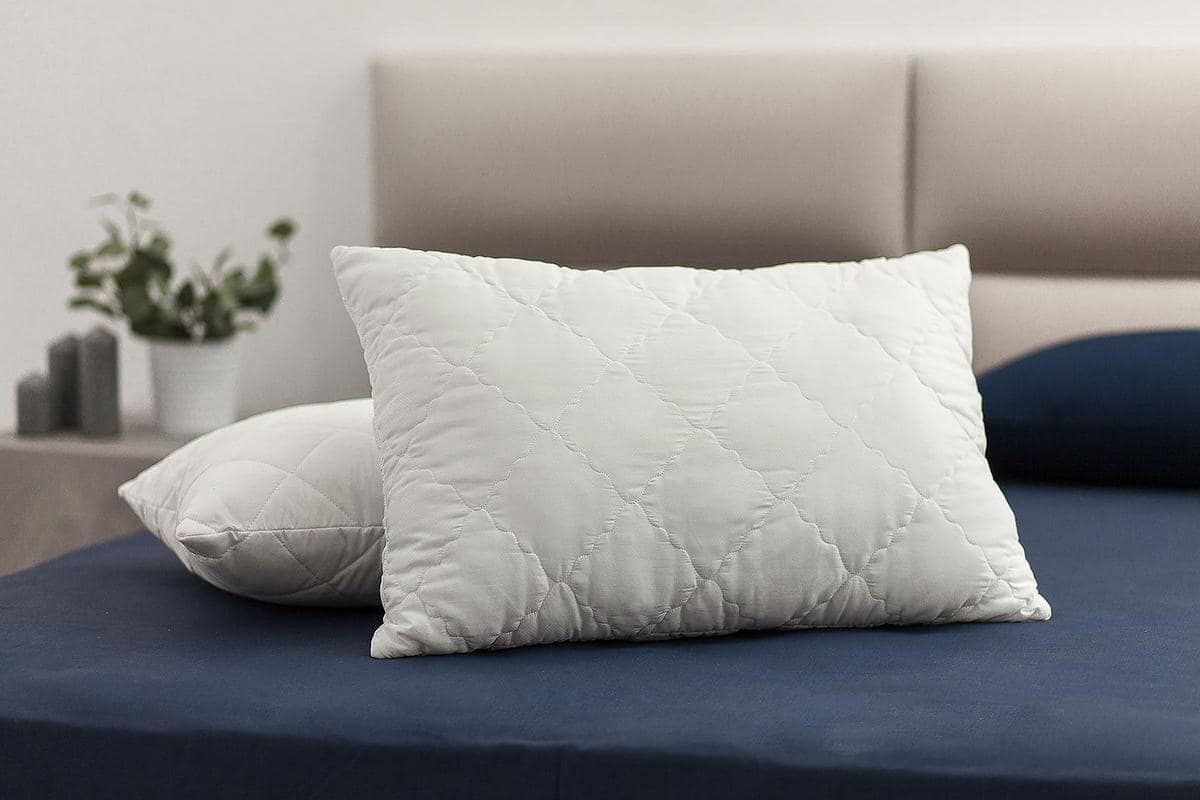
Stock Management:
Product Catalog: Create and manage a comprehensive product catalog, including variants, pricing, and availability.
Stock Levels: Track real-time stock levels for each product.
Inventory Valuation: Calculate the value of your inventory using different valuation methods (e.g., FIFO, LIFO, average cost).
Stock Adjustments: Adjust stock levels manually or automatically to account for losses, gains, or physical counts.
Product Movements:
Purchase Orders: Create purchase orders to procure products from suppliers.
Vendor Management: Manage vendor relationships, track purchase history, and negotiate terms.
Receiving: Receive products into your inventory based on purchase orders.
Sales Orders: Track products sold from your inventory through sales orders.
Delivery Orders: Create delivery orders to ship products to customers.
Returns: Handle product returns and manage refunds or exchanges.
Warehouse Management:
Warehouse Locations: Define different warehouse locations and assign products to specific locations.
Lot Tracking: Track products by lot number to manage expiration dates or traceability requirements.
Serial Number Tracking: Track products by serial number for unique items.
Barcode Scanning: Use barcode scanning to streamline inventory processes and reduce errors.
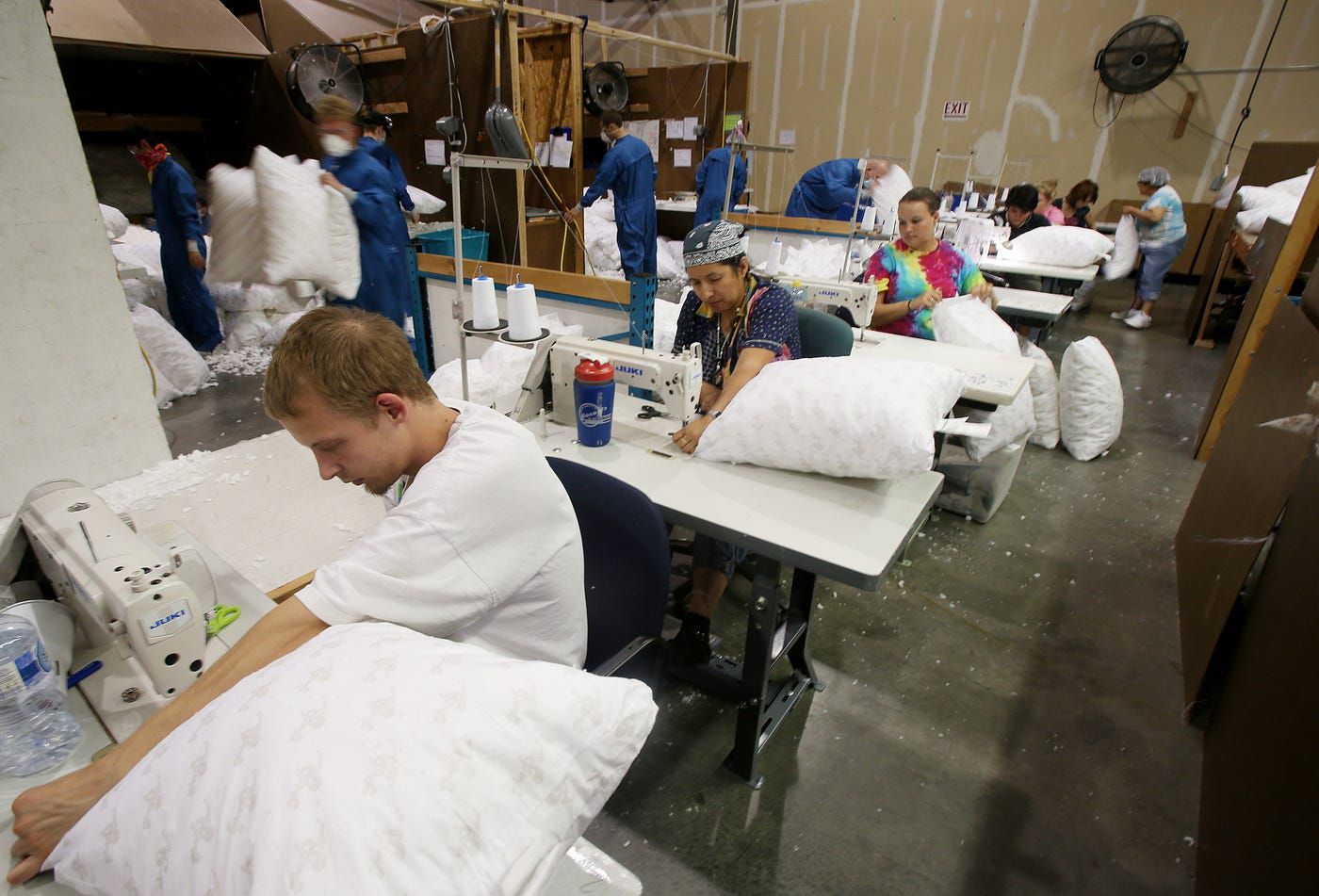
Manufacturing:
Manufacturing orders: Manage your products into assembly lines or manual assembly.
Work orders: Launch production of items needed in the final assembly of your products.
Repair orders: Manage repairs of items under warranty or as a service.
Unbilled orders: Disassemble a finished product and recuperate components.
Organize work orders: Have access to all available resources and plan with your production.
Workcenter Capacity: Use the MRP Scheduler to schedule your work at each center, based on their OEE and capacity.
Manage Bill of Materials: Keep track of the availability of items in stock and production time.
Create multi-level Bills of Materials: Set a Bill of Materials within another to manufacture components of a product in another Bill of Materials
Category:
Pillow
Type:
service
Subscription Period in Years:
1
Storage Limit:
100
Planning to Go Digital but
Not Sure Where to start?
Our expert consultants are here to guide you through the digital transformation
process. Let’s discuss how we can create a customized solution that truly transforms
your business.
Contact Us